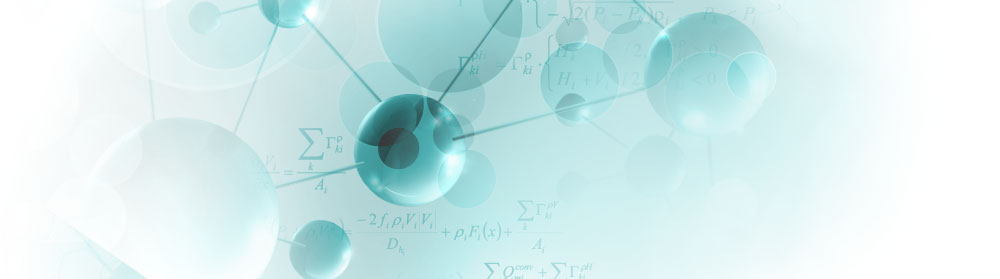
VENECIA: Venecia software package for thermal hydraulic analysis of forced flow cooled superconducting equipment and their primary cryogenic subsystems
Introduction
FROM VINCENTA TO THE ADVANCED VENECIA PACKAGE.
The software package VENECIA is the next generation of the code Vincenta offering more flexible and general application and significant innovations given rise from 10 years experience of thermal hydraulic simulations for large magnet systems (ITER, KSTAR, JT-60 and validation of code by cryogenic tests of Central Solenoid Model Coil.
Based on the original modelization approach first implemented in Vincenta, VENECIA enables numerical simulation of transient behavior of superconducting magnet systems as whole making allowance for:
- real geometry of magnet structure
- real nonlinear properties of materials
- real coolant properties
- real cryogenic accessories.
Efficient and adequate simulation is possible for both “short” transients (stability and quench of conductors etc.) and "long" transients (normal operation, warm up etc.). 01/1D models for the cryogenic circuit and 2D models for thermal diffusion in solids are coupled in a complex model to ensure comprehensive thermohydraulic analysis. The model detalization is variable over a wide range depending on the nature of problem and accuracy required.
VENECIA has benefits of an enhanced modular architecture and database approach. Each module implies a generalized algorithm for different calculation/modeling/control options. Particularly, a complex schematics is implemented for a primary cryogenic circuit that allows different modifications of control and adjustment of cryogenic parameters.
The software is now capable of simulation of up to 5 different fluids simultaneously within a single model. Databases of thermodynamic and kinetic properties of most conventional cryogenic fluids are available in the tabular format. The helium properties database is expanded to supercritical, superfluid and two-phase states. Additional databases can be synthesized from universally recognized data sources, such as CRYOSOFT HEPAK and GASPAK, and integrated into the package.
The analytical core has been substantially revised so as to provide much more efficient and stable calculations:
- the state equations now cover the superfluid He range;
- the two-phase state can be treated as a homogeneous mixture or as a gas/liquid separately, at user’s option;
- simulation of mass forces (gravity, centrifugal force) is enabled
- improved numerical stability and convergence are achiåved, primarily in the events of strong non-linearity of the thermodynamic equations in vicinity of the normal zone boundary, where substantial variations of fluid properties are observed.
- Reduced runtime
Due to extended functionality, VENECIA offers efficient solution for some intricate aspects of thermohydraulic analysis, including:
- simulations of coolant transients in superconducting magnets and their primary forced flow cryogenic circuit that includes helium circulators and cold vapor compressors for decreasing the operating temperature down to 1.8K.
- stability and normal zone propagation studies, analysis of nominal cooling conditions, and emergency situations similar to quench resulted in realise of large quantity of coolant from the magnets.
- prediction of heat load variations on the cryoplant from magnets, active mitigation of these heat variations and analysis of flow transients at inlets of rotary machines for forced flow cooling of magnets (circulator) and cold compressors for decreasing of operating temperature.
To facilitate modelization and analysis, pre- and postprocessing tools are implemented that allows visualization model linkage, meshing, real-time result monitoring, selection and plotting of outputs. However, the input procedure is kept generally unchanged so that the Vincenta users could run the code in a familiar manner. Vincenta v.6.0 files are supported.
VENECIA functionality is steadily expanded and completed so that the code evolves constantly following the practical needs giving the user a powerful tool for solving most challenging thermohydraulic problems in demand.
MINIMUM REQUIREMENTS:
- Intel Pentium IV, 1Gb RAM
- Microsoft Windows XP or higher